Группа копаний «Битруб» в составе ООО «Битруб Интернэшл» и ООО «Битруб» производит совместно на территории ФКП НИИ «Геодезия» производит методом сварки взрывом биметалл и биметаллические заготовки. О нюансах метода расскажем в этой статье.
В настоящее время в мире применяются четыре метода производства крупногабаритных листовых биметаллов (см. табл. 1).
Таблица 1. Методы производства биметаллов
№ п/п | Метод производства | Характеристика метода | Энергия расходуется | Удельный расход энергии кВт*час/м2 |
1 | Пакетная прокатка | Требуется мощное специализированное прокатное оборудование. Крупнотоннажные партии. Изготовление вакуумируемых пакетов. | Подготовка и сварка пакетов. Нагрев пакетов до температуры прокатки (1100-1200оС). Работа прокатного оборудования | 30-35 |
2 | Электродуговая наплавка | Требуются специальные установки для наплавки электродом или лентой. Требуется механическая обработка после наплавки. Деформация листов в процессе наплавки и тепловое воздействие на метал основного слоя. | Расплавление наплавочных материалов (электродов и шлака). Работа термических печей и правильного оборудования. | 199-285 |
3 | Электрошлаковая наплавка с последующей прокаткой | Требуются специальные установки для наплавки и мощное прокатное оборудование. Высокая стоимость наплавочных материалов. Ограничение по номенклатуре марок плакирующего слоя | Расплавление наплавочных материалов (электродов и шлака). Нагрев наплавленных слябов до температуры прокатки (1100-1200оС). Работа прокатного оборудования. Работа термических печей и правильного оборудования. | 120-160 |
4 | Сварка взрывом | Возможность производства любых партий биметаллов без ограничений по номенклатуре при расходном коэффициенте 1,05. Требуются специальные полигоны для ведения взрывных работ и оборудование для т.о. и правке | Абразивная зачистка свариваемых поверхностей, сборка и сварка пакетов. Работа термических печей (нагрев до 750оС) и правильного оборудования. | 3-4 |
Анализ методов производства биметалла показывает, что затраты энергии на изготовление 1 м² биметалла сваркой взрывом на порядок ниже, чем прокаткой и в 40-60 раз ниже, чем наплавкой. Низкий расход энергии при сварке взрывом связан с тем, что соединения образуется в твердой фазе и в его образовании участвуют только поверхностные слои свариваемых материалов толщиной до 0,5 мм. Следует отметить, что при получении биметаллов сваркой взрывом слои металлов, из которых они состоят, сохраняют свойства, которыми они обладали до соединения в биметалле.
Основные преимущества сварки взрывом, кроме отмеченных выше, – возможность получения прочных соединений практически любых металлов и сплавов, отсутствие ограничений по площади заготовок, относительная простота процесса и высокая производительность.
Сварка взрывом основана на принципиально новом направлении использования энергии взрывчатых веществ – не для разрушения в военном или горном деле, а для соединения двух металлов. Относительная простота процесса, возможность соединять с высокой прочностью практически любые металлы и сплавы на неограниченных плоских и криволинейных поверхностях, а также проводить работы на первых этапах освоения без значительных капитальных затрат с использованием простейшего оборудования – определили его быстрое развитие. Этому способствовали также гибкость процесса, т.е. переход от производства одного типа биметалла к другому не требует для большинства пар металлов кардинального изменения технологии.
Накопленный опыт производства биметалла сваркой взрывом убедительно показал перспективность и эффективность этого процесса, позволяющего экономить нержавеющие стали, цветные металлы и сплавы, снижать трудоемкость, стоимость изделий и повышать срок их службы в условиях воздействия агрессивных сред, создавать материалы с принципиально новыми свойствами.
В настоящее время накоплен большой экспериментальный и теоретический материал по вопросу формирования соединения при сварке взрывом, который обобщен в ряде работ. Выдвинут ряд гипотез, объясняющих образование соединения с различных точек зрения. В зоне соударения при сварке взрывом развиваются высокие давления, идет интенсивная пластическая деформация, сопровождаемая значительным повышением температуры металлов в зоне соударения. Для сварки взрывом характерны локализация в узкой зоне пластической деформации и протекание процессов рекристаллизации и оплавления. Высокие скорость пластической деформации и давление, большой градиент температур в узкой зоне, отсутствие данных по изменению свойств в таких экстремальных условиях не позволяют однозначно оценить роль в образовании соединения того или иного параметра свойств свариваемых материалов.
Образование соединения при сварке взрывом
Сварка взрывом производится в общем случае следующим образом: на песчаную опору устанавливается основной лист, над которым с определенным зазором располагается плакирующий лист с зарядом взрывчатого вещества и детонатором. После инициирования взрыва плакирующий лист под действием продуктов детонации соударяется с поверхностью изделия со скоростью 300-600 м/с. При этом образуется своеобразный канал, из которого в процессе сварки взрывом газ должен быть вытеснен.
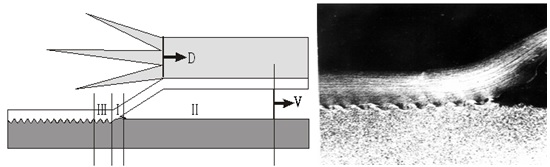
Рисунок 1. Схема сварки взрывом (а): I – зона точки контакта, II – зона впереди точки контакта, III – зона формирования соединения, D – скорость детонации, V- скорость движения УСГ. Б – вид соединения в месте остановки процесса сварки.
При метании плакирующего листа в сварочном зазоре происходит ударное сжатие газа с образованием ударной волны, которая распространяется по газу впереди точки контакта. Газ нагревается до температуры порядка 3000 К [34, 35] и вытесняется из сварочного зазора со скоростью точки контакта (2400-3000 м/с, что является гиперзвуковой скоростью). Следовательно, ударно-сжатый газ, нагретый до высокой температуры (ВУСГ), обтекает свариваемые поверхности с гиперзвуковой скоростью. Между ВУСГ и поверхностью металла образуется пограничный слой, параметры которого отличаются от свойств основного потока в связи с наличием сил трения при торможении воздуха о свариваемые поверхности и возникновения из-за наличия микронеровностей (шероховатости поверхности) турбулентности в приповерхностном слое. В этих условиях температура в пограничном слое может в несколько раз превышать ее в основном потоке ВУСГ.
Таким образом, с позиций аэродинамики при сварке взрывом в сварочном зазоре при обтекании свариваемых поверхностей с гиперзвуковой скоростью (больше 5 М) ВУСГ в пограничном слое возможно образование неравновесной ударной плазмы. По данным работы ударная плазма имеет много общего с обычной разрядной плазмой, но существуют некоторые особенности: отсутствие внешнего электрического поля, высокие температуры (Т=3000-20000 К) и наличие быстрых хемоионизационных реакций с участием возбужденных атомов и молекул.
Под воздействием ВУСГ происходит нагрев поверхностных слоев, а под воздействием ударной плазмы – очистка от окислов и загрязнений, активация поверхности. Чистые и активные поверхности вступают в контакт в точке соударения и образуют соединение, формирование которого продолжается за точкой контакта и сопровождается интенсивной пластической деформацией. Соединение имеет характерную волнообразную форму.
На сегодняшний день нет единой точки зрения на природу образования соединения при сварке взрывом, имеющего характерную волнообразную форму. Однако это не мешает ее успешному практическому применению.
Области применения биметалла, произведенного на наших предприятиях методом сварки взрывом
- Нефтехимическое машиностроение – основной массовым потребитель биметаллов с плакирующим слоем из хромистых, хромоникелевых и хромоникельмолибденовых сталей, а также хромоникелевых сплавов с основным слоем из низколегированных сталей типа 09Г2С, 12ХМ и др. Биметаллы поставляются по ГОСТ 10885 и ТУ 27.32.09.010-2005 с сертификатом качества.
- Атомное машиностроение. Биметаллы, полученные сваркой взрывом, применяются при изготовлении: теплообменного оборудования – трубные решетки конденсаторов, плакированные титаном или хромоникельмолибденовой сталью; емкости САОЗ, сепараторы пара и другие сосуды, в которых требуется защита от коррозии. В 2012 г. для изготовления оборудования АЭС нами были разработаны и согласованы в установленном порядке технические условия на биметалл 22К+08Х18Н10Т ТУ 0993-001-21414987-2012 «Лист стальной двухслойный коррозионно-стойкий, изготовленный методом сварки взрывом». Двухслойный лист, изготовляемый по этим ТУ, введен в Приложение №1 Сводного перечня документов по стандартизации НП-089-15.
- Металлургическое машиностроение. Электротехнические биметаллы: марки 09Г2С+М1 в виде листов для изготовления токоподводов рудотермических печей, марки 09Г2С+М1, М1+09Г2С+М1 для изготовления медно-стальных токосъемников (рисунок 2), двухслойные стержни марки ВТ1-0+М1 для токоподводов в электролизерах (рисунок 3) и т.п.
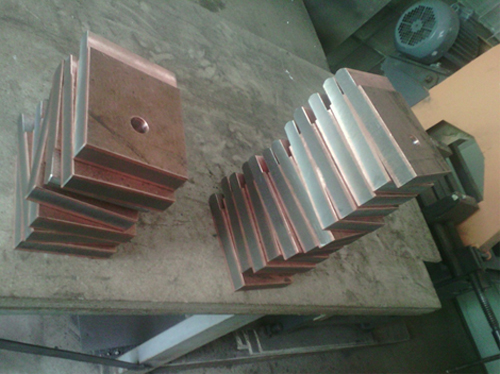
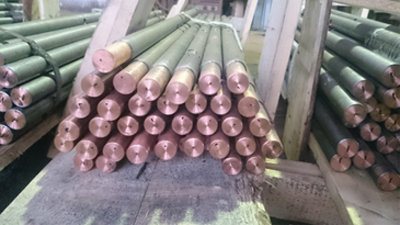
В соответствии с нормативно-технической документацией и договорами на поставку все биметаллы подвергаются следующим видам контроля:
- Визуально-измерительный контроль исходных материалов, в процессе подготовки к сварке взрывом, после получения и термообработки биметалла.
- Ультразвуковой контроль сплошности соединения после сварки взрывом и готового биметалла.
- Капиллярная дефектоскопия сварных швов плакирующего слоя в случае их наличия.
- Испытания: прочности соединения слоев на изгиб, срез и отрыв.
- Испытания основного и плакирующего слоя по требованию Заказчика.
Результаты испытаний заносятся в сертификат качества.
Высокое качество крупногабаритных двухслойных листов подтверждается исследованиями и испытаниями, проведенными в аттестованных лабораториях, результаты приведены в таблице 2. Анализ этих результатов показывает, что прочность соединения слоев на отрыв и срез превышает 250 МПа (по ГОСТ 10885 – 150 МПа). При испытаниях на изгиб биметалла сталь-титан плакирующим слоем внутрь не образуется расслоений при изгибе на 120о, а биметалла сталь-коррозионностойкая сталь – при изгибе на 160о и 180о. Большой объем испытаний показал, что свойства основного металла в процессе сварки взрывом и последующей термообработки и холодной правки не изменяются и соответствуют исходным.
Таблица 2. Результаты испытаний механических свойств биметалла и основного слоя.Марка и размеры биметалла, мм | кол. испытан-ных листов | свойства соединения | свойства основного металла | Место проведения испытаний | ||||||
σотр, МПа | σср, МПа | Боковой изгиб град. | Изгиб d=2a, град. | σв, МПа | σ0,2, МПа | δ, % | ψ, % | |||
22К+08Х18Н10Т 110(105+5)х4050х4700 | 8 | 485-578 | 292-423 | 80, УД | 160, УД | 454-505 | 221-320 | 26-31 | 58-68 | Лаборатория АО «Петрозаводскмаш» |
22К+08Х18Н10Т 60(55+5)х2500х10000 | 8 | 464-686 | 403-450 | 80, УД | 160, УД | 440-515 | 330-385 | 26-34 | 73-80 | Лаборатория АО «Дзержинскхиммаш» |
09Г2С-ВТ1-0 30(25+5)х3200х3600 | 13 | 284-428 | 221-389 | – | 120 уд | 475-580 | 315-460 | 23-35 | 71-81 | Лаборатория ИСМАН, ФГУП ЦНИИ КМ «Прометей» |
09Г2С-Grade 1 31,5(26+5,5)х3250х3700 | 14 | 363-505 | 235-378 | – | 120 уд | 510-560 | 355-425 | 27-34 | 74-83 | Лаборатория ИСМАН |
09Г2С-12+Grade 1 30(25+5)х3200х3600 | 11 | 338-497 | 214-388 | – | 120 уд | 510-560 | 355-425 | 27-34 | 74-83 | Лаборатория ИСМАН, ФГУП ЦНИИ КМ «Прометей» |
22К+08Х18Н10Т 80(75+5)х2550х4300 80(75+5)х1500х4300 | 16 | 452-608 | 488-606 | 80, уд | 160 уд | 432-479 | 320-330 | 26-33 | 72-78 | Лаборатория ООО «Зенитхиммаш» |
09Г2С+12Х18Н10Т | 2 | 557,565 | 286,395 | 80, уд | 160 уд | 493 | 282 | 29 | – | Испытательный центр «ЦНИИТМАШ-аналитика-прочность» при ОАО НПО ЦНИИТМАШ |
12ХМ+12Х18Н10Т | 2 | 449,581 | 321,480 | 80, уд | 160 уд | 508 | 275 | 27 | – | |
Ст.3сп3+ВТ1-0 | 3 | 297,347 | 250,345 | 80, уд | 160 уд | 462 | 352 | 25 | Лаборатория ПАО «Корпорация ВСМПО-АВИСМА» | |
12ХМ+08Х18Н10Т | 21 | – | 390-440 | – | 160 уд | 490-520 | – | – | – | АО «Пензахиммаш» ОГМетролога |
09Г2С-12+08Х18Н10Т | 16 | – | 330-520 | 180 | – | 500-520 | 320-420 | 21-32 | – | АО «Пензахиммаш» ОГМетролога |
09Г2С-12+10Х17Н13М2Т | 7 | – | 390-520 | 160 | – | 480-530 | 310-360 | 27-32 | – | АО «Пензахиммаш» ОГМетролога |